
PJ Forktrucks are proud to offer; Model - Still RX60-35 (latest model all AC still electric forklift, one of the best electric trucks available still rx20-20 container spec 2000kg electric forklift, linde e20, 2016, x5 stock £14,500. Electric forklifts have a tight turning radius making it an ideal forklift for small aisles. Both run by electric motor, leaving warehouses emission free, exhaust free, and noise free. Made for indoor use, these cushion tire forklifts are quiet and less expensive to run than internal combustion forklifts.

Figure 3. The battery charge gaugeindicates over-discharging. |
Only trained personnel should charge and change batteries in electric forklifts. In addition to training in battery changing and charging procedures, these employees should be trained on emergency procedures in the event of an acid splash, including how to use eyewash and shower facilities.
Potential Hazards:

- Batteries are very heavy.
- Batteries contain sulfuric acid that is highly corrosive and could be splashed on personnel servicing or changing batteries.
- Toward the end of the battery charging process, batteries can give off highly explosive hydrogen fumes.
- Contact with battery cells can cause electrical short circuits, which can burn unprotected skin.
Always follow your facility's specific safety procedures. Follow the recharger manufacturer's recommendations for attaching and removing cables and for proper operation of your equipment.

Figure 4. Electric forklift properly positioned while changing battery.
Figure 5. Battery hoistedfrom forklift compartment with lifting beam.
Figure 6. Battery charging area.
Figure 7. Eyewash station.
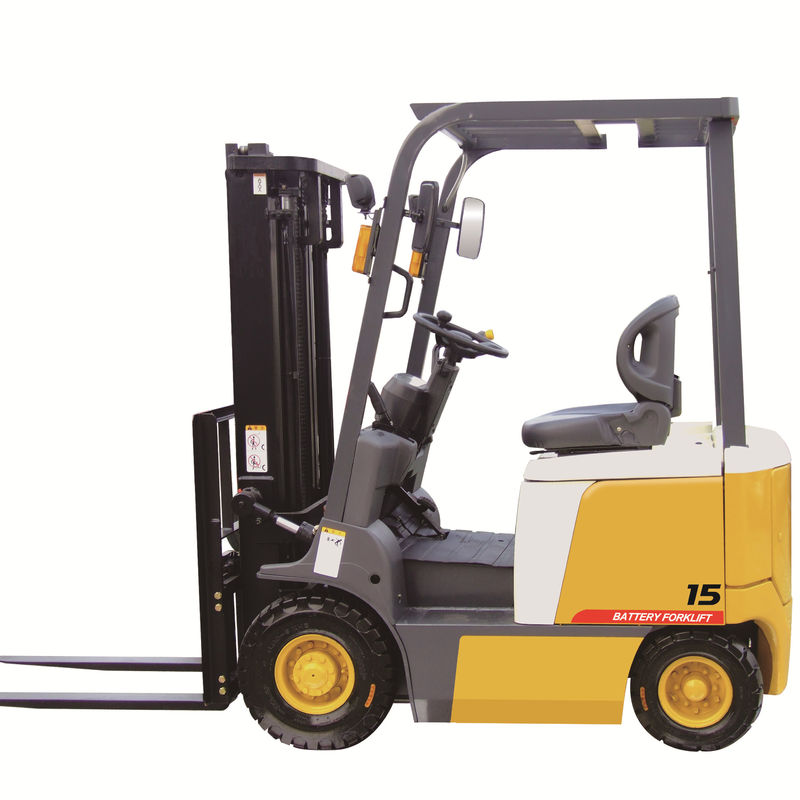
- Properly position trucks and apply brakes before attempting to change or charge batteries. (Figure 4) [29 CFR 1910.178(g)(8)]
- Use a lifting beam or equivalent material handling equipment when lifting the battery. (Figure 5) Do not use a chain with two hooks. This may cause distortion and internal damage. [29 CFR 1910.178(g)(4)]
- Charge batteries in the designated battery charging area. (Figure 6) [29 CFR 1910.178(g)(1)]
- Facilities shall be provided for flushing and neutralizing spilled electrolyte, for fire protection, for protecting charging apparatus from damage by trucks, and for adequate ventilation for dispersal of fumes from gassing batteries. [29 CFR 1910.178(g)(2)]
- NOTE: OSHA Directive, STD 1-11.4 - 29 CFR 1910.178(g)(2); Battery Charging Stations for Fork Lifts and Other Industrial Trucks, 10/30/1978 states:
'Battery charging' areas where power industrial truck batteries are charged only--no maintenance is performed, batteries are not removed from the trucks and no electrolyte is present in the area--are not subject to the requirement of [29 CFR 1910.178(g)(2)]. The charging areas shall be in compliance with [29 CFR 1910.178(g)(1), (8), (9), (10), (11) and (12)]. Personal protective equipment shall be used when and where required.
- NOTE: OSHA Directive, STD 1-11.4 - 29 CFR 1910.178(g)(2); Battery Charging Stations for Fork Lifts and Other Industrial Trucks, 10/30/1978 states:
- When charging batteries, pour acid into water. Never pour water into acid. [29 CFR 1910.178(g)(7)]
- Care shall be taken to assure that vent caps are functioning. The battery (or compartment) cover(s) shall be open to dissipate heat. [29 CFR 1910.178(g)(9)]
- Prohibit smoking in the charging area. [29 CFR 1910.178(g)(10)]
- Take precautions to prevent open flames, sparks, or electric arcs in battery charging areas. [29 CFR 1910.178(g)(11)]
- Remove all metallic jewelry before recharging. Tools and other metallic objects shall be kept away from the top of uncovered batteries. [29 CFR 1910.178(g)(12)]
- Wear personal protective equipment (face shield, safety goggles, neoprene or rubber gloves and apron). [29 CFR 1910.132]
- Where the eyes or body of any person may be exposed to injurious corrosive materials, suitable facilities for quick drenching or flushing of the eyes and body must be provided within the work area for immediate emergency use. (Figure 7) [29 CFR 1910.151(c)]
- Check the electrolyte level before recharging. Record the specific gravity with the hydrometer in the service log. Check the pilot cell.
- Check the water level. Do not add water prior to recharging. Record in service log.
- Check the voltage. If the battery has sealed vents, do not recharge with a current greater than 25 amperes.
- Unplug and turn off the charger before connecting or disconnecting the clamp connections.
- Attach the positive clamp (+, usually colored red) to the positive terminal first and then the negative clamp (-, usually colored black) to the negative terminal, keeping the proper polarity.
- Turn off the charger if the battery becomes hot or the electrolyte fluid comes out of the vents. Restart charging at a lower charging rate.
- Check water level after charging. Add distilled water or de-ionized water if water level is below level indicator. Record in service log.
- Return battery to forklift with lifting beam and secure in place after charging. [29 CFR 1910.178(g)(4) and (g)(5)]
- Check the indicator on the hour meter to see that battery is fully charged.
Worldwide, CLARK has one of the broadest product lines in the industry with five major lines. Trucks ranging from 1,500 to 18,000 pound capacities, LPG, gasoline, dual fuel, diesel, narrow-aisle stackers, electric riders and powered hand trucks.
Presently, there are over 250,000 CLARK lift trucks operating in North America and 350,000 units operating worldwide.
Electric Fork Truck Checklist
Parts Distribution – CLARK has state-of-the-art parts distribution warehouses in Louisville, Kentucky and Changwon, South Korea. The parts warehouses are centrally located to service all of CLARK’s dealers and customers.
Osha Fork Truck Training
read more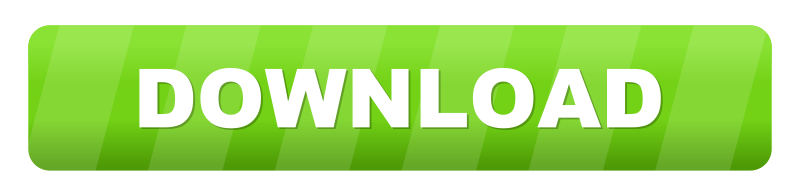